用于丹麦轨道交通建设的中国盾构机
9月29日,在位于河南郑州的中国中铁工程装备集团有限公司(以下简称“中铁装备”)盾构总装车间,一台直径8.64米的土压平衡盾构机正式下线,这是中国中铁自主研制的第1000台盾构机。这一天,车间标语“造中国人自己的盾构,造中国最好的盾构,造世界最好的盾构”显得格外醒目。
“上天有神舟,下海有蛟龙,入地有盾构”。作为“入地”利器,盾构机在某种程度上代表一国基建实力,是大国建设必不可少的核心装备。从自力更生、自主研发,到走出国门、成为亮眼的中国名片,再到突破关键技术、让民族盾装上“中国芯”,中国盾构人一路走来,着实不易。12载春秋,中铁1号到1000号,见证了以中铁装备为代表的中国企业艰苦攻关的奋斗史,更见证了国产盾构从无到有、从有到优、从优到强的逆袭历程。
历史和实践证明,技术封锁、产品垄断,只会让我们更强大。只有掌握核心技术和关键零部件,才不会受制于人。
200年前,法国工程师布鲁诺尔从一种名叫“凿船贝”的软体动物身上获得灵感,提出盾构掘进隧道原理,发明了“开放型手掘盾构”,并应用于世界上第一条水底隧道——泰晤士河水底隧道,成为人类历史上隧道施工的一大技术突破。 随着工业化水平的不断提高,机械力逐渐取代人力开挖。作为最先进的隧道挖掘机械工具,盾构机凭借快速、方便、安全的优势广泛应用于铁路、公路、地铁、市政、水电等多种隧道工程中,被誉为“工程机械之王”。盾构技术也成为衡量一个国家装备制造业水平的重要标志。 就在欧美日大力推动盾构技术升级的20世纪后半叶,基于大量基础设施建设而对盾构机有巨大需求的中国,却没有一台真正属于自己的盾构。 六七十年代,北京、上海等地的研究机构,曾在盾构机研发上取得一定突破。但受当时技术、经济等各方面条件制约,发展一直较为缓慢。 1996年12月18日,西安至安康的西康铁路开始修建,其中经过全长18.46公里的秦岭隧道。为了保障安全、缩短工期,国家以每台3.5亿元的价格从德国采购了两台盾构机。结果挖掘效率大大提升,隧道提前10个月贯通。 “洋盾构”有甜头,但越往后问题越多。买的是旧机器,却要按新设备付钱;机器维修保养时不许中方参加,还拉警戒线;维修进度中方说了不算,完全取决于外方……“有次我们要加工一个简单的拖车钢结构件,发现外方图纸有错误。因为不是设计方,只好催他们派人处理。但人家提出的条件是每天咨询费1万元,还要负责所有的差旅食宿。”中铁装备设计研究总院院长贺飞告诉记者。 没有核心技术就没有话语权,就会永远受制于人。从那时起,“造中国人自己的盾构”便成为中国盾构人的梦想。 时间进入21世纪。为打破西方技术垄断,2002年,“隧道掘进机关键技术研究”被列入“863计划”,成为国家级重点工程。由中铁隧道集团18人组成的盾构机研发项目组也于当年10月成立。 盾构机研发涵盖机械、力学、液压、电气等数十个领域,精密零部件多达3万多个,一个控制系统就有2000多个控制点。“项目组没有技术指导,从零起步,硬是从设计图纸干起。仅是弄清刀盘刀具问题,我国就花了近5年时间。”贺飞说,为了印证数据,他们不断前往施工现场求证,加班熬夜是家常便饭,通宵也是常事。 就这样,啃了6年硬骨头,在无数科研人员与专家学者的共同努力下,2008年,中国首台具有自主知识产权的复合式土压平衡盾构——中国中铁1号成功下线,后应用于天津地铁项目。至此,“洋盾构”一统天下的局面被打破了。
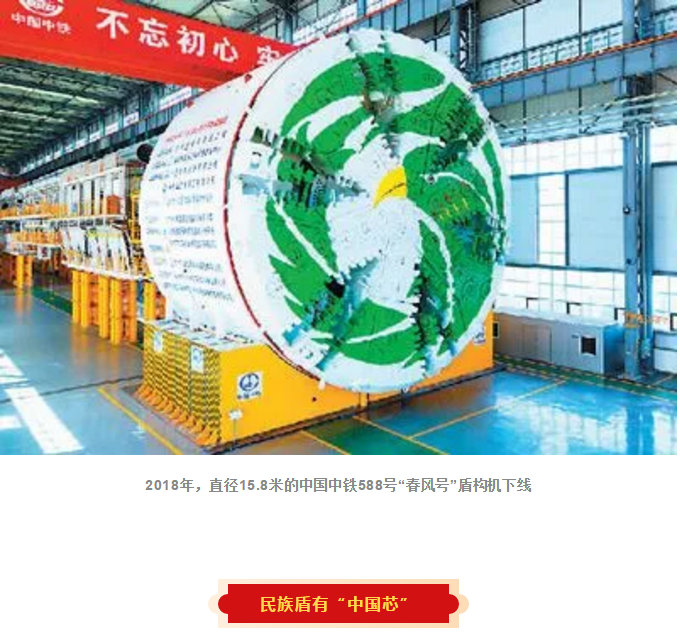
虽然有了国产盾构机,但面对国内10%的市场份额,不少人心里打鼓:国产盾构能行吗? 2012年1月,成都地铁2号线、4号线开工建设。当地地质复杂,漂石、砂卵石、涌水突出。在以往的地铁施工中,所有盾构都是国外品牌。“这并不是说进口设备在施工过程中不会出现问题,而是在当时,人们对我们自己研发的盾构机还心存顾虑。”贺飞说。 历经3个多月的交流与沟通,中铁装备团队慢慢打消了设计、施工等单位的疑虑,最终采用“1+1模式”,即国产盾构和进口盾构左右线同时始发。“这其实就给了我们一个同台较量的机会,当然要全力以赴!”此后,每名员工每天都紧张忙碌着,他们明白,这场较量不能输。 10个月后,国产盾构的各项性能指标均优于进口盾构,有力提振了中国盾构人的信心。 类似的较量还有很多。今年8月7日,中国自主研制的15米级超大直径泥水平衡盾构机克服孤石、基岩、8度地震烈度区等复杂施工条件,成功贯通汕头海湾隧道。在与进口盾构东西线两座隧道竞技过程中,国产盾构总掘进用时少了两个月。 近年来,超大断面矩形盾构、世界首台马蹄形盾构、国内最大直径土压平衡盾构、世界首台联络通道专用盾构、世界最大直径硬岩掘进机等新产品不断涌现。在与国外盾构竞争中,国产盾构在国内市场的占有率达90%以上,占全球市场份额2/3,并将同类产品价格拉低40%。 “工欲善其事,必先利其器”。盾构核心零部件关系重大,易被卡脖子。主轴承承担盾构机运转过程的主要载荷,是刀盘驱动系统的关键部件。但由于制造工艺复杂、原材料性能要求高、设计理论不成熟等原因,中国盾构主轴承长期依赖进口。 今年9月26日,在苏州轨道交通6号线10标项目现场,首台采用国产3米级主轴承盾构机“中铁872号”顺利始发,这是中国主轴承首次在轨道交通领域执行地下掘进任务。民族盾装上“中国芯”,得益于盾构/TBM主轴承减速机工业试验平台项目。 2015年7月,中铁装备联合洛阳LYC轴承有限公司和郑州机械研究所,成功申报工业转型升级国家强基工程。项目团队与时间角力,和困难较劲,终于突破主轴承、减速机设计制造关键技术。今年5月,中铁装备对通过试验检测的首批国产化6米级盾构3米主轴承、减速机进行展示,标志着中国盾构核心部件国产化取得新的重大突破,将有效降低对关键部件进口的依赖。
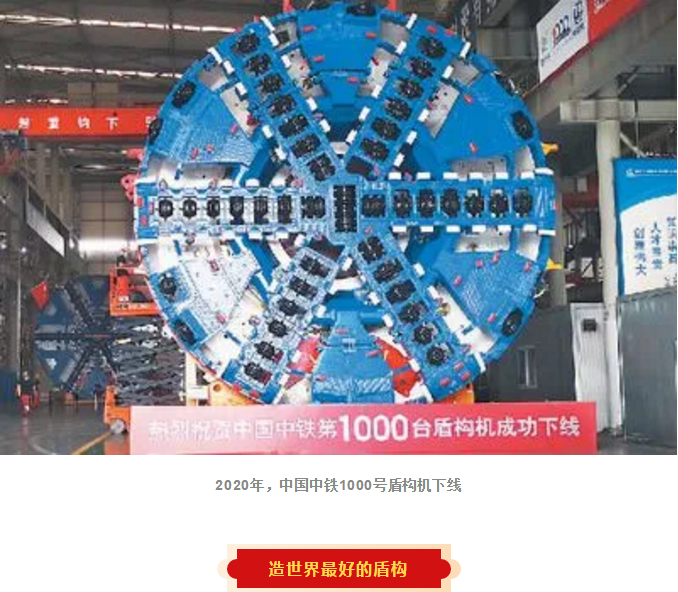
要不断提升中国盾构的竞争力和影响力,就不能止步于国内搭台比试。 马来西亚,是中铁装备迈出国门第一站。2012年,马来西亚正在推进MRT项目(马来西亚捷运线)。一期工程时,承包该项目的中铁国际集团马来西亚公司主动向马方推荐中铁装备生产的盾构机。 然而,马方对中国盾构并不信任,直言不讳道:“你们在中国做得好,但在海外市场没有经验,我们对你们非常担心。”即便如此,中方团队仍不停地往返于中马两国,向马方介绍中国盾构的发展历程,并邀请他们来华实地考察。 “中国盾构的发展速度令人惊奇!”这是代表团考察后发出的感慨。随后,马方决定购买两台中国盾构机,即“中铁50号”“中铁51号”。 施工中,“中铁50号”曾遇到一块20多米长的孤石,其硬度达到300兆帕,远远超出地质报告所提的砂岩、泥岩不到80兆帕,但它凭借可靠的性能通过了考验。其兄弟“中铁51号”表现也很突出,不仅先后穿越具有百年历史的中央火车站等重要建筑物,将最大累计沉降量控制在3毫米内,还创造了最高日掘进21米的当地盾构施工新纪录。 马来西亚项目的成功,为中铁装备走向世界、迎接更大挑战打下坚实基础。 2015年,黎巴嫩政府实施大贝鲁特供水项目,以解决当地民众饮水难题。与之前大体型的盾构机不同,此次工程要求的TBM直径仅为3.53米。 2016年1月,中铁装备自主研制的两台世界最小直径硬岩掘进机下线。这是黎方首次使用全自动TBM施工,他们还专门为两台机器命名:“丽雅”“雅斯米纳”,代表慷慨、正直、开放和勇敢、果断、活力。 “我们再也不用购买桶装水喝了!”2018年3月2日,随着工程2号隧洞最后一片岩块轰然碎地,在场的当地民众一片欢呼。2019年,整个引水隧洞项目投入使用,基本解决贝鲁特用水问题,约160万人从中受益。 准确满足各国客户需求,是更好走出去的关键。2019年8月,两台由中铁装备研发制造的盾构机出口丹麦,应用于哥本哈根CRSH1地铁项目,实现中国盾构首次进入北欧。 在欧洲,丹麦被公认为标准高、制度严,该项目由两家世界顶级土建承包商承包。“他们有非常丰富的施工经验,对于安全高效施工,有着自己的理解,所以对盾构机的设计方案也有很多细节要求。”中铁装备副总经理张志国谈到,我们坚持以客户关注为焦点,定制化打造盾构机,往往更容易受到海外市场青睐。 目前,中铁装备的盾构机已出口至全球21个国家和地区,连续3年产销量世界第一。“中国盾构已实现从‘跟跑’向‘并跑’和部分‘领跑’的转变,未来要在智能化上更进一步,让整个隧道实现自动化建造,这是我们努力的方向。”贺飞表示。
评论区已关闭。