装载机是中国工程机械行业中具有优势市场地位的一款细分产品。装载机作业工况复杂,如何确保高效生产和低油耗,优化装载机驱动特性和降低油耗是该应用的关键技术之一。针对该应用,丹佛斯开发了2MT双马达静液压驱动系统,由单泵双马达组成闭式传动系统。
▌该系统的特点在于其性能可进行参数化调整,满足不同使用场合。而参数化调整的本质在于对速度、扭矩等参数进行调节并对各元件进行逻辑控制。该系统参数匹配度高,实际调试过程中,需要不断调整参数及其之间的匹配关系,进行实车验证、分析、测试、优化,该过程需要投入大量时间及资源。由此,我们需要建立对应的仿真系统,以减少调试时间,提高工作效率。
▌通过建立该系统的仿真模型,在Matlab/Simulink仿真环境下进行参数匹配及调试,然后进行实车参数验证及优化,可以减少调试时间,加速系统开发。同时也可以根据系统模型计算油耗和功率,对比车辆在不同工况下的油耗。因此,以丹佛斯应用开发中心 5吨装载机为仿真对象,对该车辆的行走系统进行建模及仿真。建模思路:
进行建模仿真之前,需明确系统的工作原理,并将整个系统划分为子系统或者几个组成部分,如液压系统、机械传动部分、控制模块等。根据仿真目的,对复杂且重要性不高的环节进行一定程度的简化,逐一搭建子系统模型,并导入系统参数进行调试。通过对仿真与理论或实验结果进行对比分析,可以验证模型的准确性,以及进一步优化模型。
系统建模过程1) 一泵两马达闭式液压系统
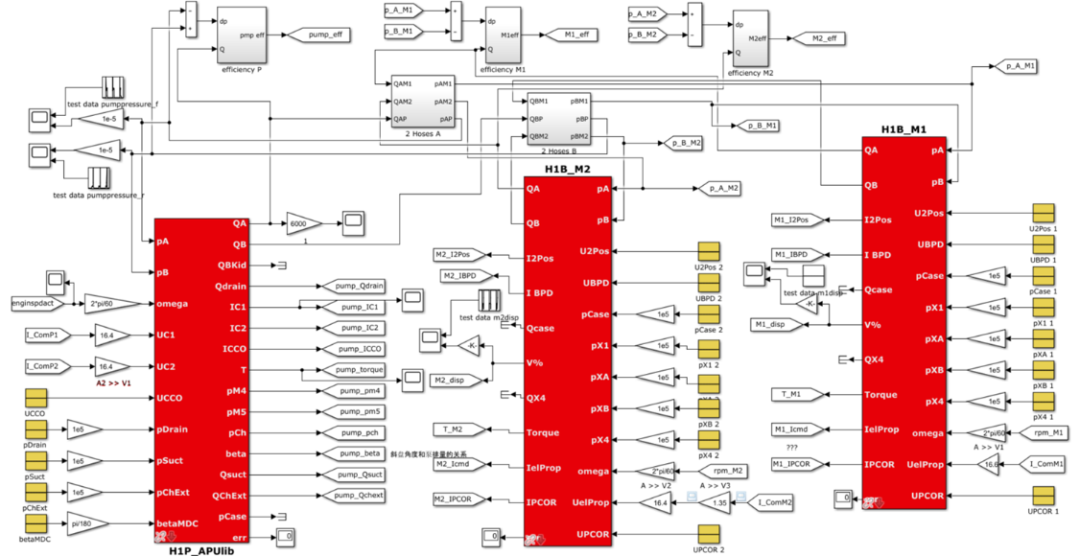
▌基于系统原理,建立H1P、H1B元件模型,以及一泵两马达闭式液压系统模型。泵马达均为电比例控制方式,通过给定不同的控制电流信号及泵轴转速等参数,进行模型调试。根据泵马达的输入、输出功率关系,计算其效率。
2) 发动机、变速箱及负载模型▌ 建立发动机模型,并输入map图以及实际负载扭矩,可以得到准确的油耗仿真结果。变速箱模型是实现2MT和1MT模式切换的核心元件,离合器脱开时,马达2转速为零且无扭矩输出。负载模块的核心思想是对车辆行驶的过程进行受力分析,计算实时车速以及变速箱输出转速,同时可以计算变速箱的输出功率和能耗,结合液压系统功率损失、发动机油耗,分析整个系统的能耗分布。
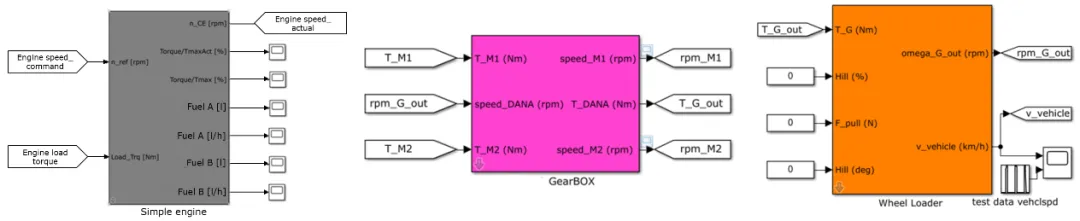
3) 控制模块
▌控制模块主要包括外部输入信号,内部控制逻辑,输出信号三部分组成。输入信号包括油门踏板、挡位模式和FNR信号,输出信号包括泵、马达电流、发动机请求转速、离合器控制信号。内部控制逻辑包括油门信号与发动机请求转速的profile设定;发动机转速与泵控制电流的Profile设定;马达控制电流与系统流量的Profile设定;车辆前进/后退模式的控制逻辑;实时车速与离合器脱开/结合的判断逻辑。
4) 参数设置▌子系统调试完成意味着整个系统的建模基本完成,然后输入车辆的实际参数,进行模型调试。由于该模型涉及的参数较多,且含有多个数组,因此,从外部导入参数至Matlab,然后在模型中设置变量名称,可以方便调用和更改。
· 仿真与实验结果的对比分析
在相同条件下,对车辆进行仿真和实车测试,进行仿真与测试结果的对比分析。输入条件为车辆一档前进,一段时间后停止。
▌整体来看,在相同的输入条件下,仿真与实验结果的一致性较好,尤其是静态特性,两者的数值基本吻合。起动和停止的动态过程中,仿真与测试结果的曲线变化趋势相同,数值略有偏差。发动机实际转速与泵控制电流的静态特性与实验吻合度高,系统高压侧压力略高于实验结果。
▌动态特性的影响因素较多,一方面与发动机的动态特性有关,另一方面与起动瞬间车辆的实际负载突变有关。实际上,输入的参数越全面,建立的模型越准确。对于不能直接获取的参数,可以通过仿真与测试结果的对比分析,对现有参数进行优化和调整,并在不同工况下进行验证,使模型精确度进一步提高。
输入不同的发动机map图,可以计算不同的发动机油耗:
▌我们以丹佛斯应用开发中心5吨装载机为仿真对象,对2MT双马达静液压驱动系统进行建模及仿真分析。通过仿真,可以进行系统参数的匹配,效率分析及逻辑验证。参考其动态特性可以掌握参数的变化趋势及变化量,为后续的系统开发奠定了理论基础,仿真与测试结果的稳态特性误差不超过5%。此外,通过建立仿真模型,先在仿真环境下进行参数匹配及调试,在此基础上进行实车验证及优化,可以缩短系统开发及调试周期,节省30%以上的调试时间。通过变更输入参数,还可以计算不同工况下系统功率损失和发动机油耗,分析整个系统的效率。
评论区已关闭。